UNDERSTANDING STYRENE AND CIPP
By NASSCO member Tony Araujo, Vice President – Business Development, Paragon Systems Testing
In the more than 50 years since its invention, cured-in-place pipe (CIPP) has become a very popular and cost-effective trenchless pipe rehabilitation technology. The ability to choose from a wide variety of resin chemistries/felt/ reinforcement systems allows CIPP users to tailor an individual rehabilitation solution to the specific conditions present within a particular installation to ensure a long-lived structural solution. While this advantage allows users to solve a broad range of rehabilitation problems, the final manufacturing of a CIPP is performed in the field, and this inherent feature also creates conditions which must be considered in any CIPP QA/QC program.
When developing a QA/QC program for a CIPP project, a good place to start is NASSCO’s Performance Specification Guideline (PSG) Cured- In-Place Pipe (CIPP) Installation. The PSG is developed with expertise from a wide range of industry experts and in addition to detailing specific terminology guidance also provides additional context notes within text boxes, when necessary, allowing the user to better understand the background behind the guidance.
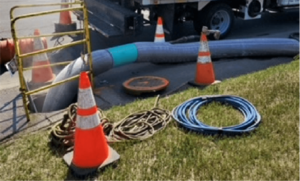
The PSG defines two mechanical properties which must be met by finished CIPP, these are flexural modulus and flexural strength.
Additionally, the wall thickness must meet or exceed that specified in the CIPP design. These three characteristics are all affected by the nature of field installation. This is sometimes referred to as natural variation. The PSG states:
“The mechanical properties and physical characteristics of the finished CIPP will vary considerably, depending on the types and mixing proportions of the materials used and the degree of cure executed.”
To ensure that the finished CIPP exhibits the necessary properties, field samples are prepared during installation which are then sent to a testing laboratory for testing of the actual installed properties. Two types of field samples are defined, restrained samples and plate samples. Restrained samples are made by passing the impregnated tube through a cylindrical mold which is the same diameter as the sewer being rehabilitated. Plate samples, used in larger diameter installations when restrained samples may be unpractical, are made by sandwiching a sample of the impregnated felt material between two metal plates. Both types of samples are cured along with the installed CIPP as defined in ASTM F1216. The laboratory prepares test specimens from these field samples and then tests them for flexural modulus and flexural strength. The laboratory also measures wall thickness from the restrained sample. Since plate samples can be made in any thickness, wall thickness can be confirmed by measurements of the actual CIPP by collecting a small core sample from within the CIPP. NASSCO’s CIPP PSG, referenced above, also describes a quality-based approach for determining thickness compliance when only plate samples are collected, typically large diameter installations.
When one or more of these properties fails to meet those specified in the contract because of natural variation, the CIPP may need to be repaired or replaced, but only after a closer review of the CIPP design and the laboratory test results. Frequently, when one of these properties is found to be lower than specified, say wall thickness, the flexural properties may be higher than specified which may then compensate for the lower thickness and vice versa. When an initial review, normally performed by the contract administrator, does not resolve the discrepancy, an evaluation can look more closely at the CIPP design and the actual installation conditions. This review process is called reconciliation.
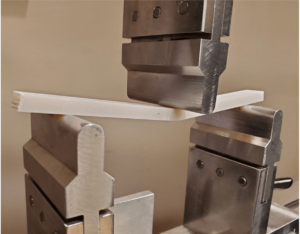
Obviously reconciling the issues resulting from natural variation and ensuring that every CIPP complies with the contract requires field sample testing data. For this reason, many owners sample and then test each installed CIPP. For larger projects this can result in a logistics and data management headache if not planned for prior to project kick-off. Physical samples need to be acquired from specific locations, identified appropriately, the chain of custody established, transportation to a laboratory coordinated, testing results prepared and then distributed to the necessary individuals, and finally the data itself then needs to be reviewed and actioned appropriately. One way to ensure that this process runs smoothly and cost effectively is using automation as much as possible and also by keeping all data, both collected from the field and generated in the testing laboratory, in digital form. Communication with the testing laboratory early in the tender preparation process will ideally establish which elements of the whole process that they will be responsible for and how information will be collected, analyzed and distributed.
“Natural variation is just that, natural. With good planning and appropriate preparation, it shouldn’t be a headache to deal with.”
TECH TIPS IS A BI-MONTHLY ARTICLE ON TRENDS, BEST PRACTICES AND INDUSTRY ADVICE FROM NASSCO’S TRENCHLESS TECHNOLOGY MEMBERSHIP PROFESSIONALS
Follow us on social media or visit NASSCO.org